By Natalia
On a recent trip to New York City, I was very excited to visit an operating flower factory, Custom Fabric Flowers by M&S Schmalberg. I have been following them on Facebook and love all the new creations that they post. They said they offer tours of their flower factory, so I made an appointment and stopped in to see how the magic is created!
When I arrived, I was greeted by Adam who is the son in this 4th generation, family owned company. The show room was filled with all kinds of examples of the flowers they make, but there would be time for browsing later. We left the show room and headed straight to the area where the flowers are made. It turns out that making flowers in a factory is very similar to making flowers by hand. The individual steps are very similar. The factory has large machinery to help, but it’s still a very labor intensive process. The first step is to stiffen the fabric. It’s stretched on the racks below, sprayed with stiffener and left to dry.
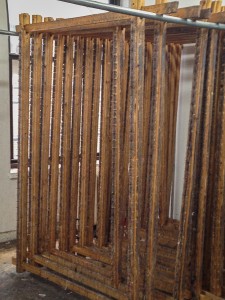
Next, the die is chosen for cutting out the shape of the flower petals. There were literally hundreds of dies! You can see on the top shelf of the photo below that some of the dies have a large post on them. In the past, multiple layers of fabric would be set up, the die placed on top, and a hammer would be used to cut out the shape.
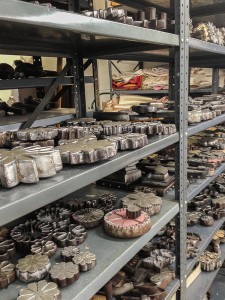
Thanks to modern machinery, hammers are no longer necessary. The left shot below is of one of two machines that they have for cutting out the shapes. The process is still the same: layer the fabrics, place the die, then swing the arm over both and the arm presses down to cut out the shapes. The photo on the right shows an employee cutting out some flowers.
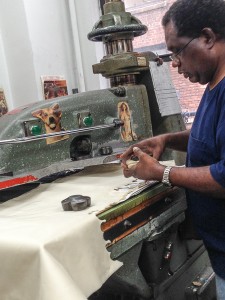
The factory also has a dye room and I got to see that too. As you can see in the photo below on the left, the petals have been cut out at this stage and the edges are being dyed. The fabric could have been dyed first too. For example, I picked up some lovely velvet flowers that had been tie-dyed in rich blues and greens. These are definitely one of my great finds.
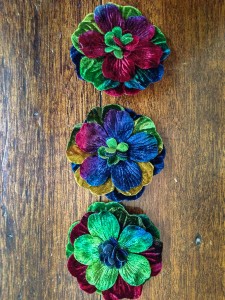
From here, the flowers need to be shaped. There are equally as many molds (photo on the left) to choose from, each with a top and bottom, or male and female part, to shape the flowers. Historically, a manually operated machine was used, shown below on the right. The tabletop is heated (so the whole thing was radiating heat), the bottom of the mold was placed on the table underneath the big wheel, the top of the mold was placed in the shaft, and the wheel was turned to create the pressure needed to form the shape. As you can imagine, this was also very labor intensive and not an enjoyable job since you are working over the equivalent of a hot stove all day. Today, this is used to keep the molds warm while the workers shape other flowers.
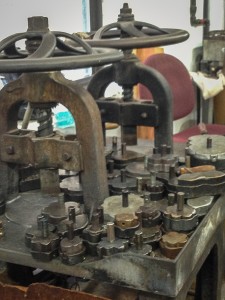
To shape the flowers, they now use a heated hydraulic press, but it is the same process. The bottom of the mold goes in the middle of the plate, the top of the mold with the shaft goes in the top of the machine. One flower petal is placed on the bottom part of the mold. With the push of a button, the top comes down, holds for a few seconds to shape the petal, and then it releases. The worker places the shaped petal in his ever-growing collection of shaped petals!
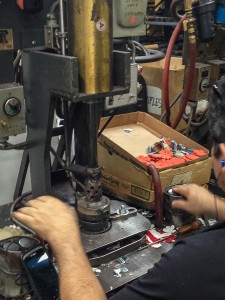
From here, the flower is assembled. A number of ladies were taking wire and stamens as needed, gluing the petals to the wire, and letting them dry. You can see the individual petals on the table and the completed flowers hanging from the line above.

After the tour, I met Warren, the father in this family owned business. I got to look through all the flowers that they had in stock (hundreds!) and pick some out to take home with me. Warren told me the stories about the flowers I chose (many hand dyed, some based on Dior flowers, etc). He also shared a treasure chest full of flower making tools from a company that went out of business. So many interesting tools!
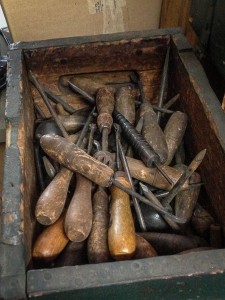
If you are in New York City, I highly recommend stopping by Custom Fabric Flowers and checking it out! They are located at 242 West 36th Street, 7th Floor, New York, NY 10018.
By Natalia
Cocktail hat with black sinamay circular base, adorned with handmade purple feather flower, black ostrich feather, purple guinea feathers, and black and metallic purple crin.
By Natalia
Cocktail hat with black sinamay pillbox shaped base, adorned with loops of cream sinamay and cream stripped coque feathers. Hat is secured with an elastic band that goes under the hair. One-of-a-kind, handmade hat using traditional millinery techniques.
By Natalia
A weekend of millinery workshops with Jenny Pfanenstiel of Formé Millinery! Please note the following:
- All workshops require a minimum of 4 people registered by September 13th to run.
- All workshops will have a maximum of 8 people.
- Register for all five workshops and save $150!
- Refunds will only be offered if a workshop is cancelled.
- REGISTER HERE: http://www.brownpapertickets.com/event/406201
Making a Royal Wedding Fascinator
2 day workshop
Friday, September 20th, 10:00am-12:00pm
Saturday, September 21st, 10:00am-1:00pm
$275.00 per person
Have you ever wondered how to make the hats that you see Kate Middleton or Lady Gaga wear? In this two-day course, we will take sinamay and block it on “disk” blocks that sit atop your head. We will then embellish them and finish with elastic or headbands. One size fits all. Materials are included (sinamay, wire, elastic, headbands). Bring basic sewing supplies (scissors, thread, needle, pins) and glasses for close up work if needed. Also bring any embellishments you may have (broaches, feathers, flowers) to incorporate into your hat. No millinery experience required.
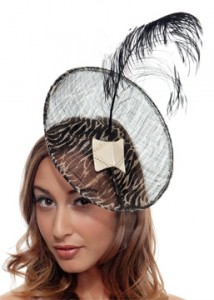
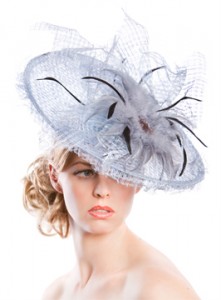
Free Form Wool
1 day workshop
Friday, September 20th, 1:00pm-5:00pm
$195.00 per person
Does your style take on a more abstract look and feel? This course takes hat making to the next level without using hat blocks. You will learn how to take straw/wool and by using a head form as a base, you will twist, turn, fold, and manipulate the material to create a beautiful abstract hat piece. We will then finish the hat with wiring (if needed) and create a base (if needed) for your hat to sit on. All materials are included. Attendees need to bring a styrofoam head (or canvas wig head), water bottle, sewing kit and any embellishments. No millinery experience required.
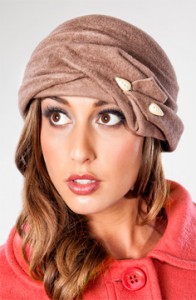
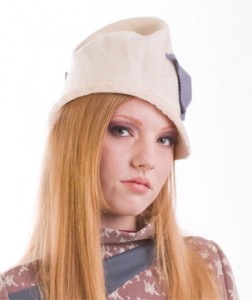
Straw Braid Oh My!
1 day workshop
Saturday, September 21st, 2:00pm-7:00pm
$195.00 per person
In this workshop, you will get your creative juices going by making your own straw braid! Straw braid bases for hats do not need to be boring and basic just because it sits underneath your embellishments. Think color and texture. Your base should be a part of your hat and we are going to do just that! We will start with many different types of straw, yarn, and miscellaneous materials to braid into our straw braid. Then we will take our straw braid and hand sew it into many different types of bases. Once completed, we will finish the hat with an assortment of embellishments. Attendees need to bring a sewing kit, styrofoam head (or canvas wig head) and embellishments. Straw braid kits will be provided. No millinery experience required.
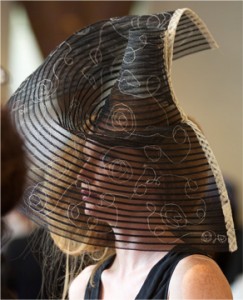
Carving Your Own Hat Block
1 day workshop
Sunday, September 22nd, 10:00am-4:00pm
$165.00 per person
Does buying $300 hat blocks break your bank? Or are you looking for that special hat block that doesn’t exist? Why not make your own! Each person will sketch a hat that they would like to make and/or bring pictures from magazines of hats. From that sketch, each person will sculpt a block out of styrofoam to resemble the shape. We will start with carving the basic shape with a knife and finish by using sandpaper to smooth down the edges to resemble blocks in the industry. This is a great class to create that hat form you have always envisioned in your head but cannot find as a block. Each person will need to bring a hot glue gun, glue sticks and a straight edge knife for carving. I will supply the block making material and sand paper.
“Block”ing Party
1 day workshop
Sunday, September 22nd, 5:00pm-8:00pm
$160.00
Let’s have a “block”ing party!! Have you ever just wanted to have access to many different blocks and just BLOCK and then finish them at home? Now is your chance. Come mingle, have some wine and hors d’oeuvres and block away. 2 wool hoods or 2 wool capelines will be provided, all of the hat blocks galore and refreshments! Additional hoods and capelines will be available for purchase. You must know how to finish a hat on your own.
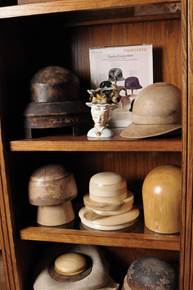
About Formé Millinery
Jenny Pfanenstiel, International Award Winning Couture Milliner and Owner of Formé Millinery, makes handmade hats for women, gentlemen and children. Her one-of-a-kind hats are created using age old techniques of steaming and blocking over hat blocks as a true Couture Milliner once did. In addition to using age old techniques, Jenny has mastered the art of hand manipulation of traditional and nontraditional millinery materials creating “sculptures” for the head. Jenny is a Milliner that creates hats for the modern person with an old soul.
As a Milliner, she has become known for her dedication to quality and taking once admired materials from the country roads in France, to the outback in Australia and incorporating these pieces to truly make one-of-a-kind pieces. “As a Couture Milliner, my goal is to make a person feel sensational in my hats. I want them to look into the mirror and feel transformed, almost as if they are one with the creation of the hat.”
You can find her collections in specialty boutiques around the world and in magazines such as Vogue, Tatler, Country Living, Vigore and Belle Armoire. Her hats have been featured on The Oprah Show and are owned by First Lady Michelle Obama. Jenny is a repeat guest and shows her hat collections often at The Drake Hotel, Woman’s Athletic Club and Service Club of Chicago events. She is also a featured Milliner for the Derby showcasing her hats at Keeneland, The Kentucky Derby Museum, Galt House, Les Filles, Equus Run Vineyards and many Kentucky TV stations and magazines.
Millinery is a craft that Jenny wants to keep alive. She teaches Couture Millinery instruction around the world in group and private workshops, including basic blocking on antique hat blocks, to sculptural hats using Jinsin.
Jenny is on the Board of Directors for the Apparel Industry Board and Fashion Group International, a member of the Milliners Guild in NY, member of the Headwear Association, a 2012 FGI Rising Star Winner, and a two time Winner of the Hatty Award (an International award given to Milliners).
www.formemillinery.com
By Natalia
Hand-blocked saucer hat with feathers and beading on one side, feather flowers on the other side. Hat is sewn to a head band wrapped in black satin ribbon.